Home > Composites > Aluminum Sandwich Panel
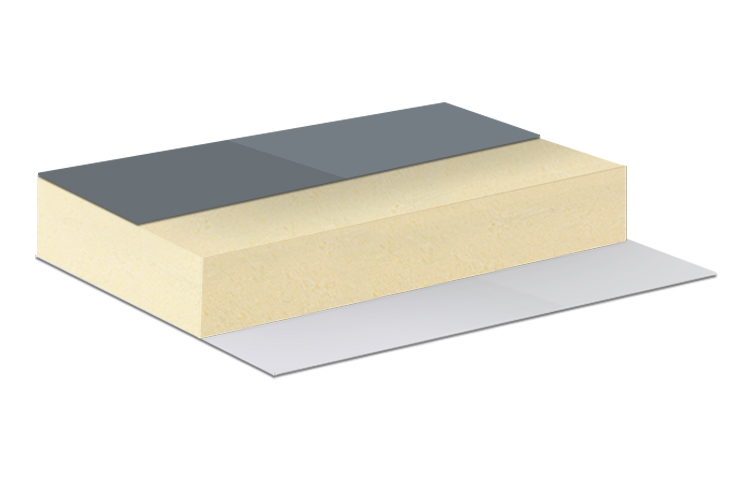
Aluminum sandwich panels are a composite material consisting of two layers of aluminum plates and a sandwich core material. The aluminum plate provides external structural support and has excellent corrosion resistance and oxidation resistance, while the core material gives the sandwich panel excellent properties such as lightweight, thermal insulation, and sound insulation.
Common core materials of aluminum skin sandwich panels include polystyrene (XPS), polyvinyl chloride (PVC) and polyethylene terephthalate (PET). These materials have their own characteristics and are suitable for different usage scenarios. .
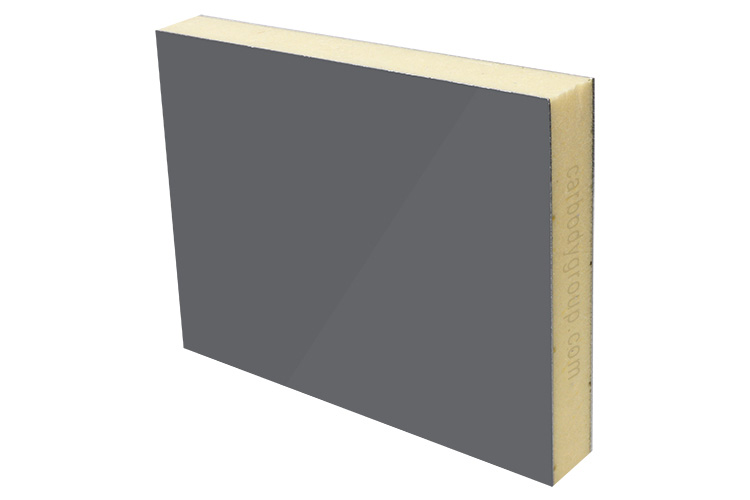
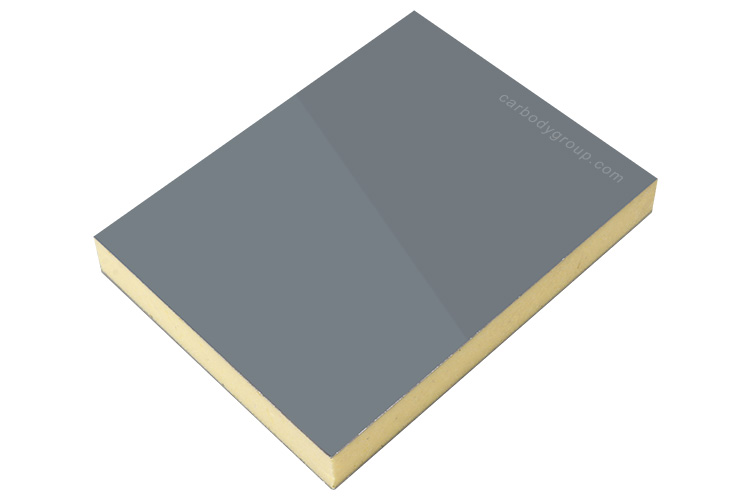
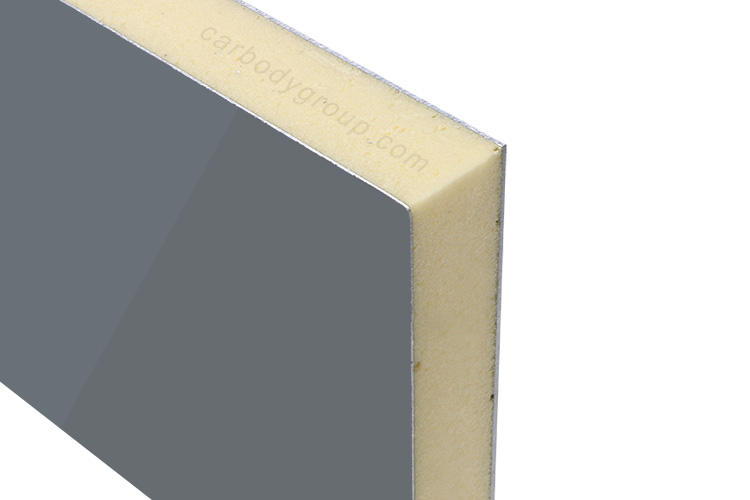

Structure and Composition
The basic structure of an aluminum foam sandwich panel includes three layers: two outer aluminum sheets and a central foam core. The aluminum sheets provide the panel with its structural integrity, durability, and resistance to corrosion. These sheets can be coated or treated to enhance specific properties like UV resistance or fire retardancy.
The core material, often made of PU or XPS foam, offers excellent thermal insulation due to its low thermal conductivity. This foam core also contributes to the overall lightweight nature of the panel, making it easier to handle and install.
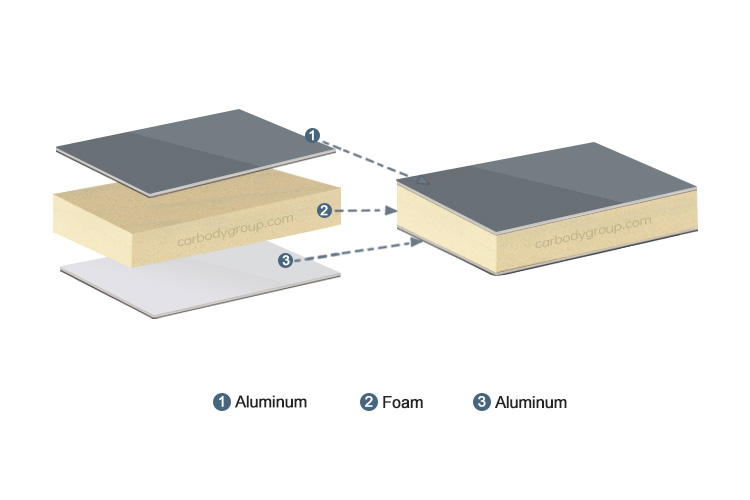
Painted Aluminum Sheet
Aluminum is lightweight, corrosion-resistant and machinable, and with the enhancement of surface coating, it has excellent weather resistance and decorative properties.
Aluminum alloy grade
- 1050、1060、3003、3004、5052、5005、5083、6061
Surface coating
- Polyester (PE) coating
- Fluorocarbon (PVDF) coating
Surface color
- White, gray, black
- Yellow RAL series
Size
- Thickness: 0.1-3.0mm.
- Width: ≤2600mm.
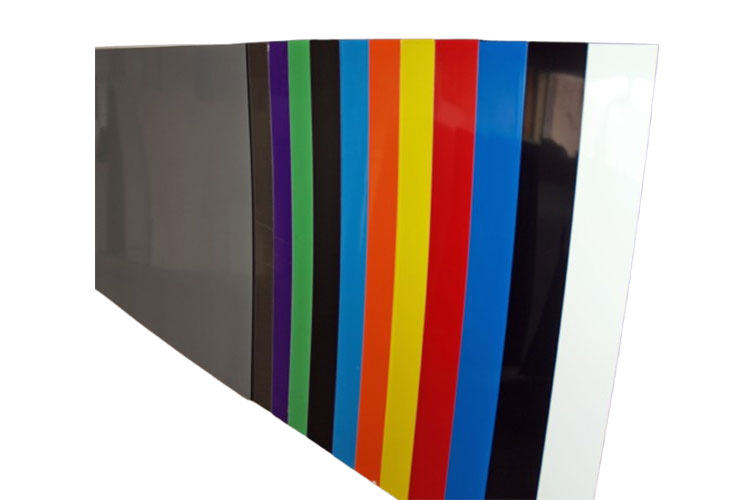
Types of Foam Cores
Polyurethane (PU) Foam
Polyurethane is a premium thermal insulation material that can be customized from 20 to 120mm in thickness. It has excellent thermal and acoustic insulation properties, making it ideal for applications where temperature control is critical, such as refrigerated trucks and cold rooms.
Using aluminum as the outer skin has advantages. It can improve its compression resistance and stability. It is less prone to deformation and is stronger.
It can also be used with FRP. This makes it a high-strength, bending-resistant, high-performance composite panel. It can operate in temperatures from -40°C to 100°C. It will not deform.
Extruded Polystyrene (XPS) Foam
XPS (Extruded Polystyrene) foam is a rigid closed-cell foam insulation material. It has high compressive strength and moisture resistance.
Advantages
- Lightweight: The foam core significantly reduces the weight of the panel, making it easy to handle and install.
- Thermal Insulation: Both PU and XPS foams have low thermal conductivity, providing excellent insulation.
- Durability: The aluminum sheets provide resistance to corrosion and environmental factors. The panels can withstand harsh weather conditions.
- Easy to Process: Aluminum foam sandwich panels can be easily cut and processed using our high-precision CNC tools.
- Customizable: Panels can be customized in thickness, length, width, and color.
Application Fields of Aluminum Sandwich Panels
- Box Trucks
- Box Trailers
- Modular Buildings
- RVs